Let’s get started with Variable Frequency Drive working, also known as VFD. It is an electronic device that controls the speed of electric motors by adjusting the frequency of the electrical power supplied to them. These drives have become increasingly popular in recent years due to their energy-saving capabilities, improved process control, and reduced wear and tear on motors.
Variable Frequency Drives Explained:
A variable frequency drive has various other names like adjustable-frequency drive AFD, adjustable speed drive ASD, variable speed drive VSD, AC drive, micro drive, inverter drive, or motor drive is a type of AC motor drive that controls speed and torque by varying the frequency of the input electricity. Depending on its topology, it controls the associated voltage or current variation. Unlike fixed-speed motors that operate at a constant speed, VFDs enable dynamic control of motor speed, allowing it to match the required load demand.
This incredible device allows for the precise control of motor speed and offers a multitude of benefits, ranging from energy efficiency to improved process control. In this blog, we will dive into the inner workings of VFDs, explore their advantages, and understand their wide-ranging applications.
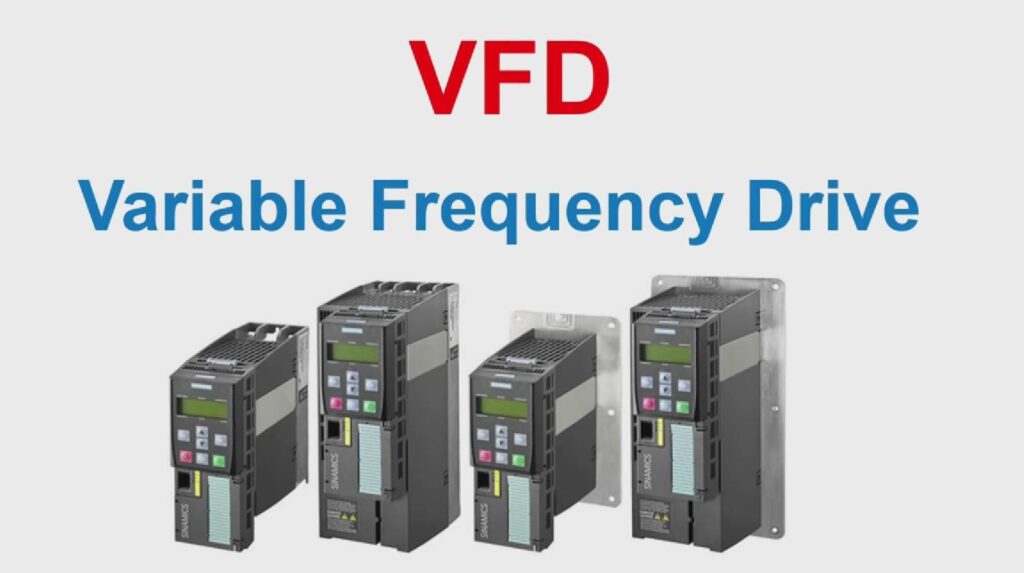
How do Variable Frequency Drive work?
You can see variable frequency drive working with block diagram. VFDs operate on the principle of converting the incoming fixed-frequency alternating current (AC) power into direct current (DC) and then re-converting it back into AC power with variable frequency and voltage. This process involves three key components:
Rectifier: The rectifier stage converts the AC power supply into DC power by rectifying the incoming AC waveform. It typically employs diodes or thyristors to achieve this conversion.
DC Bus: The DC bus acts as an intermediate storage for the converted DC power. It smooths out any fluctuations and provides a constant voltage source for the next stage.
Inverter: The inverter stage takes the DC power from the DC bus and converts it back into AC power with a variable frequency and voltage output. It uses semiconductor devices, such as insulated gate bipolar transistors (IGBTs), to create the desired waveform.
Control circuit: This includes a microprocessor unit that performs various functions like control, configuring drive settings, fault conditions, and interfacing communication protocols. It receives feedback signal from the motor and accordingly regulates the ratio of voltage to frequency to adjust motor speed.
Variable Frequency Drive Block Diagram:
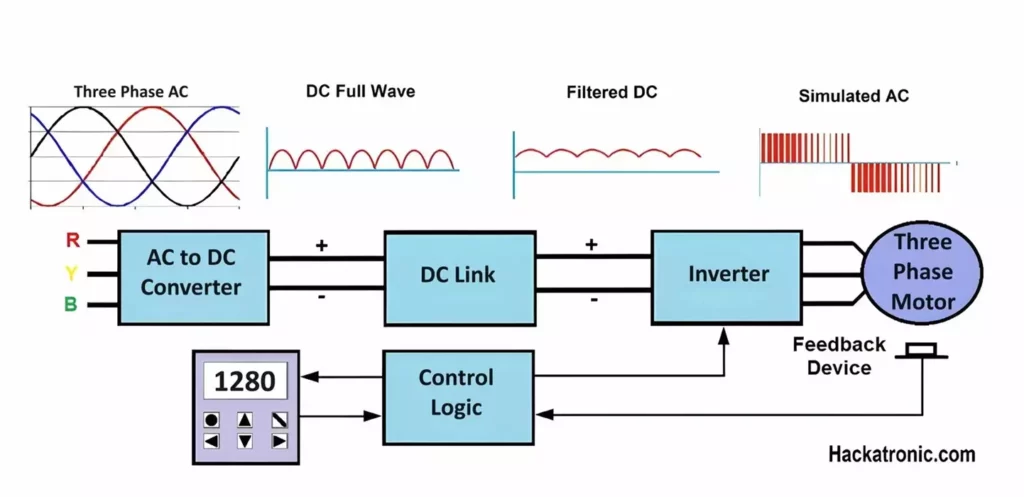
By adjusting the frequency and voltage of the output AC power, VFDs precisely control the motor speed. This flexibility provides numerous advantages and applications across various industries.
Advantages of Variable Frequency Drive:
Energy Efficiency: One of the most significant benefits of VFDs is their ability to optimize energy consumption. By adjusting the motor speed to match the required load, VFDs eliminate the energy wastage associated with fixed-speed motors running at full capacity, even when it’s unnecessary. This efficient operation translates into substantial energy savings and reduced operating costs.
Soft Start and Stop: VFDs offer a soft start and stop function, gradually ramping up the motor speed and reducing mechanical stress. This feature reduces wear and tear on equipment, extends the motor’s lifespan, and enhances overall system reliability.
Precise Control and Flexibility: VFDs provide precise speed control, allowing motors to operate at varying speeds as per process requirements. This level of control enhances productivity, improves process accuracy, and enables finer adjustments in applications such as robotics, conveyors, and pumps.
Reduced Mechanical Stress: By gradually accelerating the motor and minimizing torque spikes, VFDs reduce the mechanical stress on the motor and connected machinery. This results in smoother operation, reduced maintenance, and lower chances of equipment failure.
Applications of Variable Frequency Drives:
Variable Frequency Drives (VFDs) have a wide range of applications across various industries due to their ability to control motor speed and provide energy efficiency.
Let’s explore some common applications where VFDs are extensively used:
HVAC Systems:
Heating, ventilation, and air conditioning (HVAC) systems often employ VFDs to control the speed of fans and pumps. By adjusting the motor speed according to the required airflow or water flow, VFDs help maintain optimal comfort levels while reducing energy consumption.
Industrial Processes:
VFDs find extensive use in industrial applications where precise control of motor speed is crucial. Industries such as manufacturing, food processing, textile production, and material handling rely on VFDs to regulate the speed of conveyor belts, mixers, compressors, and other equipment. This enables improved process control, energy efficiency, and enhanced productivity.
Water and Wastewater Treatment:
VFDs play a vital role in water and wastewater treatment plants. They are used to control pumps, blowers, and aerators, ensuring the right amount of water flow or air supply at various stages of the treatment process. By adjusting motor speeds based on demand, VFDs optimize energy consumption and reduce operational costs.
Renewable Energy Systems:
VFDs contribute to the efficient operation of renewable energy systems such as wind turbines and solar power plants. In wind turbines, VFDs adjust the generator speed to optimize power output based on wind conditions. For solar power plants, VFDs regulate the speed of motors driving solar trackers, which orient the solar panels to maximize sunlight absorption.
Oil and Gas Industry:
VFDs are extensively used in the oil and gas industry for controlling pumps, compressors, and drilling equipment. By adjusting motor speed based on real-time requirements, VFDs ensure optimal performance and energy efficiency in drilling operations, pipeline transportation, and refinery processes.
Elevators and Escalators:
VFDs provide precise control and energy efficiency in vertical transportation systems. In elevators and escalators, VFDs regulate motor speed to match passenger demand, resulting in smooth acceleration, deceleration, and reduced energy consumption during idle periods.
Electric Vehicles:
VFDs are an integral part of electric vehicle (EV) propulsion systems. They control the motor speed, torque, and regenerative braking, enabling efficient energy usage and extending the vehicle’s range.
Machine Tools:
VFDs enhance the performance and energy efficiency of machine tools, such as milling machines, lathes, and CNC machines. By adjusting motor speed during different machining operations, VFDs provide flexibility, precision, and power savings.
These are just a few examples of the diverse applications of Variable Frequency Drives (VFDs). Their ability to control motor speed, improve energy efficiency, and enhance process control makes them an integral component in numerous industries, contributing to cost savings, reduced environmental impact, and overall operational optimization.
Types of Variable Speed Drives: Construction, Working & Applications
Revolutionary Axial Flux Printed Circuit Board (PCB) Stator Motor
Thank you very much.
it’s very helpful
Thanks , this article help me .